Nickelage
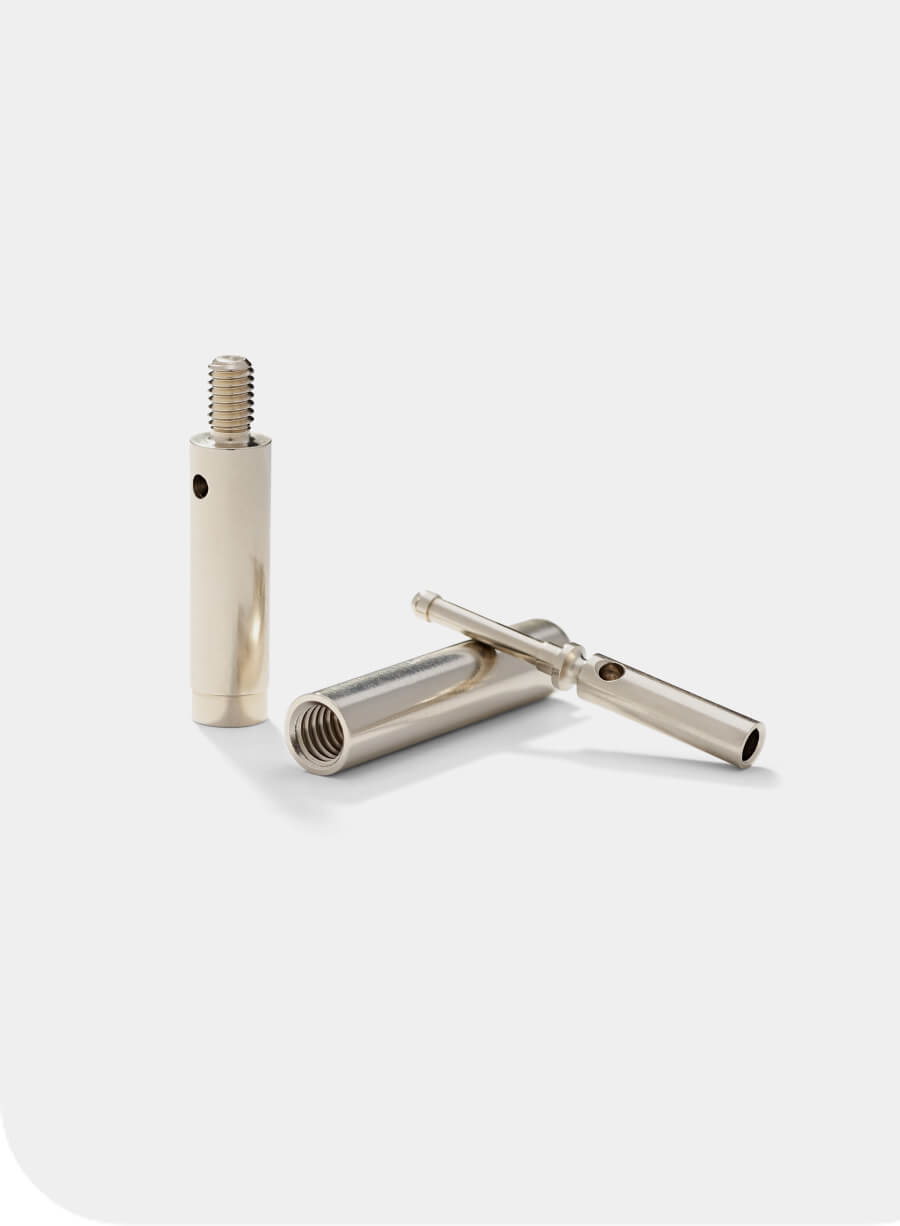
Nickel
Symbole chimique : Ni
Le nickelage électrolytique consiste à déposer une couche de nickel sur une pièce via électrolyse, en utilisant des solutions aqueuses composées de divers sels. Ce procédé permet d’améliorer les performances des pièces traitées, notamment en les protégeant contre la corrosion, tout en offrant un aspect brillant et esthétique.
Dans le domaine de la connectique, le nickel électrolytique est souvent utilisé en sous-couche avant l’application de dépôts d’or, d’étain ou d’argent. De plus, le nickelage améliore la résistance des pièces à des températures élevées.
Caractéristiques du dépôt de nickel
Le nickel est plus électropositif que les substrats sur lesquels il est déposé, tels que l’acier. Par conséquent, si la couche de nickel présente des imperfections ou est perforée, la corrosion du substrat sera favorisée.
Le nickel présente une excellente résistance à la corrosion grâce à sa capacité à se passiver, c’est-à-dire à former rapidement une couche protectrice d’oxyde de nickel, empêchant ainsi une corrosion destructive.
Traitements particuliers
À Electrolyse Abbaye d’Acey, nous employons principalement un bain de sulfate de nickel mais nous utilisons également d’autres types de traitements :
Nickel de Wood
Notre traitement est utilisé exclusivement comme sous-couche d’accroche pour les pièces en inox qui recevront un autre dépôt par la suite.
Sulfamate de nickel
Les bains à base de sulfamate de nickel [Ni(NH2SO3)2] sont prisés pour leurs faibles contraintes internes, permettant des dépôts de fortes épaisseurs à des vitesses élevées.
Caractéristiques
Physiques | |
---|---|
Densité (kg/dm3) | 8,9 |
Température de fusion (°C) | 1455 |
Résistivité électrique (µohm.cm) | 9,2 |
Conductivité thermique (cal.cm/cm².s.°c) | 0,18 |
Mécaniques | |
Plage de dureté EAA (HV) | 130 – 200 |
Température limite d’emploi (°C) | 900 |
Applications
→ En couche finale et dépôt épais pour résister à la corrosion de différents produits chimiques et éviter la corrosion par fretting
→ En sous-couche dans les revêtements d’or ou d’argent pour les pièces subissant d’importants frottements et pour éviter la diffusion entre le substrat et le dépôt final
→ En couche barrière entre le laiton et l’étain pour éviter la diffusion du zinc dans l’étain ou entre tous types de substrats et l’étain pour limiter la génération de whiskers
→ En couche finale pour apporter des caractéristiques esthétiques à la pièce et une bonne résistance à des températures élevées
Foire
aux questions
1
Quels paramètres influencent la qualité du dépôt lors du nickelage électrolytique ?
Plusieurs paramètres doivent être contrôlés pour obtenir un dépôt de nickel de haute qualité:
- Densité de courant : La quantité de courant appliquée affecte la vitesse et la qualité du dépôt. Des densités de courant trop élevées peuvent entraîner des défauts comme des dépôts rugueux ou des bulles.
- Température du bain : La température influence la vitesse de dépôt et la qualité du revêtement. Les températures typiques sont entre 40°C et 60°C.
- pH de la solution : Le pH doit être maintenu à un niveau optimal pour éviter la précipitation de nickel ou la formation de défauts. Il est généralement contrôlé autour de 3 à 5 pour les solutions de sulfate de nickel.
- Concentration des ions : La concentration en ions de nickel dans la solution doit être surveillée pour garantir un dépôt uniforme et éviter les variations de qualité du revêtement.
2
Quels sont les traitements post-nickelage courants pour améliorer la qualité du dépôt ?
Après le nickelage électrolytique, plusieurs traitements peuvent être effectués pour améliorer la qualité du dépôt :
- Passivation : Un traitement chimique qui forme une couche protectrice supplémentaire sur le nickel pour améliorer sa résistance à la corrosion.
- Polissage : Pour améliorer l’apparence esthétique, les pièces nickelées peuvent être polies pour obtenir une finition plus lisse et brillante.
- Rinçage et séchage : Un rinçage minutieux et un séchage approprié sont essentiels pour éviter les résidus de solution et garantir une finition de haute qualité.
3
Quels sont les principaux avantages du nickelage électrolytique ?
- Résistance à la corrosion : Le nickel forme une couche protectrice qui protège le substrat contre la rouille et la corrosion.
- Amélioration de la dureté : Le dépôt de nickel durcit la surface, améliorant ainsi la résistance à l’usure et à la friction.
- Adhérence : Il améliore l’adhérence des couches de revêtements ultérieurs, comme l’or.
- Aspect esthétique : Le nickelage peut fournir une finition lisse et brillante, souvent utilisé pour des applications décoratives.
- En sous couche pour éviter la diffusion du substrat dans la couche finale